Unveiling the Heart of Modern Transportation: A Deep Dive into Internal Combustion Engines
Uncategorized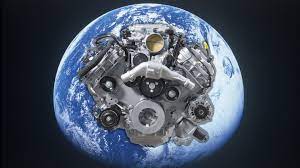
Introduction
• Brief overview of the importance of internal combustion engines in modern society.
• Mention of their prevalence in automobiles, aircraft, ships, and power generation.
History of Internal Combustion Engines
• Overview of early experiments and inventions leading to the development of internal combustion engines.
• Key milestones: Otto, Diesel, and other pioneers.
• Evolution from simple designs to complex, high-performance engines.
Working Principles
The working principle of an internal combustion (IC) engine involves a series of controlled explosions within a confined space to convert chemical energy from fuel into mechanical energy.
1. Intake Stroke:
The engine cycle starts with the intake stroke.
in intake valve opens, and the piston moves downward, Air (in a spark-ignition engine) or air-fuel mixture (in a compression-ignition engine) is drawn into the cylinder from the intake manifold.
2. Compression Stroke:
After the intake stroke, the intake valve closes, and the piston moves upward, compressing the air or air-fuel mixture.
The compression increases the pressure and temperature inside the cylinder, preparing it for combustion.
3. Power Stroke:
When the piston reaches the top of its stroke, the spark plug (in a spark-ignition engine) ignites the air-fuel mixture, or the fuel self-ignites due to high compression (in a compression-ignition engine).
The rapid combustion of the fuel-air mixture generates a high-pressure force that pushes the piston downward.
This downward motion of the piston is harnessed as mechanical energy.
4. Exhaust Stroke:
The upward movement expels the burned gases from the combustion chamber through the open exhaust valve.
This completes one cycle of the engine, and the process repeats continuously as long as the engine is running.
Key Components:
Piston: Moves up and down inside the cylinder to compress the air-fuel mixture, and to convert the energy from combustion into mechanical motion.
Cylinder: Enclosed chamber where the piston moves, and where combustion occurs.
Valves: Intake and exhaust valves control the flow of air or air-fuel mixture into the cylinder and the exhaust gases out of the cylinder, respectively.
Spark Plug (in SI engines): Generates a spark to ignite the air-fuel mixture.
Fuel Injector (in CI engines): Injects fuel into the cylinder at high pressure for compression ignition.
Crankshaft: Converts the linear motion of the piston into rotational motion, which is used to drive the vehicle or machinery.
Efficiency and Variants:
The efficiency of an IC engine depends on factors like compression ratio, combustion efficiency, and mechanical losses.
Variants include two-stroke engines (with intake, compression, power, and exhaust strokes in only two movements of the piston) and four-stroke engines (as described above).
Understanding the working principle of IC engines is crucial for appreciating their role in various applications, from automobiles and aircraft to power generation and industrial machinery.
Fuel Systems:
1. Carburetor System:
Function: Historically common in older vehicles, carburetors mix air and fuel in the correct ratio before entering the engine’s cylinders.
Operation: Airflow through the carburetor creates a low-pressure area, drawing fuel from the fuel bowl and atomizing it into the airstream.
Advantages: Simplicity, low cost.
Disadvantages: Less precise fuel-air mixture control, lower efficiency, higher emissions.
2. Fuel Injection System:
Function: Modern fuel injection systems deliver precise amounts of fuel directly into the engine’s cylinders or intake manifold.
Types:
Port Fuel Injection (PFI): Injects fuel into the intake ports before the intake valves.
Direct Injection (DI): Injects fuel directly into the combustion chamber.
Advantages: Improved fuel efficiency, better performance, reduced emissions.
Disadvantages: Higher cost, complexity.
Ignition Systems:
1. Spark Ignition (SI) System:
Function: Used in gasoline engines, the SI system ignites the air-fuel mixture in the combustion chamber with a spark from a spark plug.
Components:
Spark Plug: Produces the spark to ignite the air-fuel mixture.
Distributor (in older systems): Distributes high-voltage electricity from the ignition coil to each spark plug.
Ignition Coil: Converts low-voltage battery power into high-voltage electricity needed to create the spark.
Advantages: Precise control of ignition timing, smoother engine operation.
Disadvantages: Requires maintenance (e.g., spark plug replacement), limited ignition timing flexibility.
2. Compression Ignition (CI) System:
Function: Commonly used in diesel engines, the CI system ignites the fuel-air mixture by compressing it to a high temperature and pressure.
Components:
Glow Plug: Heats the air in the combustion chamber to facilitate combustion during cold starts.
Fuel Injector: Injects fuel into the combustion chamber at high pressure.
Advantages: No need for a spark plug, higher efficiency due to higher compression ratios.
Disadvantages: Typically heavier and more expensive than SI systems, limited to diesel engines.
Modern Advancements:
Electronic Fuel Injection (EFI): Replaces carburetors with electronically controlled fuel injectors for precise fuel delivery and combustion control.
Direct Injection (DI): Improves fuel efficiency and performance by injecting fuel directly into the combustion chamber.
Electronic Ignition Systems: Replace traditional distributor-based systems with electronically controlled ignition timing for better performance and fuel economy.
Understanding the fuel and ignition systems of IC engines is crucial for optimizing performance, fuel efficiency, and emissions control in modern vehicles and machinery. Advances in these systems continue to drive improvements in engine technology, making vehicles cleaner, more efficient, and more reliable.
Performance:
1. Power Output:
Displacement: Larger engines typically produce more power due to increased displacement, which allows for greater combustion of air and fuel.
Compression Ratio: Higher compression ratios result in more efficient combustion and increased power output.
Forced Induction: Turbocharging or supercharging increases air intake, allowing the engine to produce more power by burning more fuel-air mixture.
2. Torque:
Torque Curve: A broad and flat torque curve provides better low-end torque, improving acceleration and drivability.
Variable Valve Timing (VVT): Adjusting valve timing optimizes torque output across different engine speeds and loads.
3. Fuel Efficiency:
Combustion Efficiency: Complete combustion of fuel-air mixture maximizes energy extraction and fuel efficiency.
Thermal Efficiency: Efficient conversion of heat energy from combustion into mechanical work.
Engine Design: Features like lightweight materials, reduced friction, and aerodynamic design enhance fuel efficiency.
Electronic Engine Management: Advanced engine control units (ECUs) optimize fuel delivery, ignition timing, and other parameters for improved efficiency.
Efficiency:
1. Thermal Efficiency:
Carnot Efficiency: Theoretical limit on the efficiency of heat engines based on the Carnot cycle.
Actual Efficiency: Real-world efficiency of IC engines typically ranges from 20% to 40%, with diesel engines generally more efficient than gasoline engines.
2. Mechanical Efficiency:
Friction Reduction: Minimizing frictional losses through improved lubrication, smoother surfaces, and tighter tolerances.
Reciprocating Components: Reducing energy losses from the reciprocating motion of pistons, connecting rods, and crankshafts.
3. Emissions Control:
Catalytic Converters: Reduce harmful emissions by converting pollutants like carbon monoxide (CO), hydrocarbons (HC), and nitrogen oxides (NOx) into less harmful substances.
Exhaust Gas Recirculation (EGR): Reduces NOx emissions by recirculating exhaust gases into the combustion chamber to lower combustion temperatures.
Selective Catalytic Reduction (SCR): Reduces NOx emissions in diesel engines by injecting urea into the exhaust stream to convert NOx into nitrogen and water.
Advances and Future Trends:
Hybridization: Combining IC engines with electric motors to improve efficiency and reduce emissions.
Alternative Fuels: Exploring biofuels, hydrogen, and synthetic fuels as cleaner alternatives to conventional gasoline and diesel.
Advanced Engine Designs: Researching innovations like opposed-piston engines, variable compression ratio engines, and homogeneous charge compression ignition (HCCI) for improved efficiency.
Electrification: Increasing adoption of electric vehicles (EVs) alongside IC engines to reduce dependence on fossil fuels and mitigate environmental impact.
Understanding the performance and efficiency characteristics of IC engines is essential for optimizing their operation, reducing emissions, and advancing sustainable transportation solutions in the future. Continuous research and development efforts aim to push the boundaries of efficiency while minimizing environmental impact.
The performance and efficiency of internal combustion (IC) engines
Factors influencing engine performance: displacement, compression ratio, and combustion efficiency.Methods for enhancing engine performance: turbocharging, supercharging, and variable valve timing. Discussion on fuel efficiency and the role of engine design and technology in achieving higher miles per gallon (MPG).
Environmental Impact
Addressing the environmental concerns associated with internal combustion engines.
Emissions of greenhouse gases (CO2) and pollutants (NOx, particulate matter).
Introduction of emissions control technologies: catalytic converters, exhaust gas recirculation (EGR), and selective catalytic reduction (SCR).
1. Air Pollution:
a. Criteria Air Pollutants:
Nitrogen Oxides (NOx): Generated during combustion, NOx contributes to smog formation, acid rain, and respiratory issues.
Particulate Matter (PM): Fine particles emitted from IC engines, especially diesel, can penetrate deep into the lungs and cause respiratory and cardiovascular problems.
Carbon Monoxide (CO): Colorless, odorless gas produced by incomplete combustion, CO is toxic and can impair oxygen delivery in the body.
b. Volatile Organic Compounds (VOCs):
Unburned hydrocarbons released from IC engines contribute to the formation of ground-level ozone and smog, leading to respiratory issues and environmental damage.
2. Greenhouse Gas Emissions:
a. Carbon Dioxide (CO2):
Mainly produced from the combustion of fossil fuels in IC engines, CO2 is a major contributor to global warming and climate change.
b. Methane (CH4) and Nitrous Oxide (N2O):
IC engines also emit small amounts of methane and nitrous oxide, which are potent greenhouse gases with significantly higher global warming potentials than CO2.
3. Noise Pollution:
IC engines, especially in vehicles and industrial machinery, generate noise pollution that can impact human health, wildlife, and ecosystems.
4. Resource Depletion:
Extraction and consumption of fossil fuels for IC engines contribute to resource depletion and environmental degradation through activities like drilling, mining, and transportation.
Mitigation Strategies:
a. Emissions Control Technologies:
Catalytic Converters: Reduce NOx, CO, and hydrocarbon emissions by converting them into less harmful substances.
Particulate Filters: Trap and remove particulate matter from diesel exhaust.
Exhaust Gas Recirculation (EGR): Reduces NOx emissions by recirculating exhaust gases into the combustion chamber.
Selective Catalytic Reduction (SCR): Converts NOx emissions into nitrogen and water using a urea-based additive.
b. Fuel Efficiency Improvements:
Advancements in engine design, such as turbocharging, direct injection, and variable valve timing, improve fuel efficiency and reduce emissions.
Hybridization and electrification technologies combine IC engines with electric motors to further enhance efficiency and reduce reliance on fossil fuels.
c. Alternative Fuels:
Transitioning to cleaner alternative fuels like biofuels, hydrogen, and synthetic fuels can reduce emissions and lessen the environmental impact of IC engines.
Applications
1. Automotive Transportation:
Cars: IC engines power the majority of passenger vehicles worldwide, providing mobility for individuals and families.
Trucks and Commercial Vehicles: Heavy-duty diesel engines propel trucks, buses, and commercial vehicles for transporting goods and passengers over long distances.
Motorcycles: IC engines are the dominant power source for motorcycles, offering fuel efficiency and performance.
Aviation:
Aircraft: IC engines, particularly piston and turbine engines, are used in general aviation, small aircraft, helicopters, and some military aircraft for propulsion.
Unmanned Aerial Vehicles (UAVs): Many drones and UAVs utilize small IC engines for propulsion, enabling various applications such as surveillance, agriculture, and aerial photography.
Marine:
Boats and Ships: IC engines, including diesel and gasoline engines, power a wide range of watercraft, from small recreational boats to large cargo ships and naval vessels.
Power Generation:
Generators: IC engines, often running on diesel or natural gas, are employed as standby or primary power generators in residential, commercial, and industrial settings to provide electricity during power outages or in remote locations.
Combined Heat and Power (CHP) Systems: IC engines can be integrated into CHP systems to simultaneously generate electricity and utilize waste heat for heating or cooling purposes, improving overall energy efficiency.
Industrial Machinery:
Construction Equipment: IC engines power construction machinery such as excavators, bulldozers, loaders, and cranes, providing the necessary torque and mobility for various construction tasks.
Agricultural Machinery: Tractors, harvesters, and other agricultural equipment often rely on IC engines for propulsion and powering implements.
Off-Road Vehicles:
ATVs and UTVs: All-terrain vehicles (ATVs) and utility task vehicles (UTVs) commonly feature IC engines for off-road recreational and utility purposes.
Military Vehicles: IC engines are used in military vehicles such as tanks, armored personnel carriers, and logistics vehicles for mobility and power.
Stationary Equipment:
Pumps and Compressors: IC engines drive pumps and compressors in various applications, including water pumping, oil and gas extraction, and industrial processes.
Stationary Engines: IC engines are utilized in stationary applications such as irrigation pumps, emergency backup systems, and industrial machinery.
Conclusion:
Internal combustion engines play a critical role in powering a wide range of vehicles, equipment, and machinery across industries, enabling transportation, electricity generation, and industrial processes essential for modern society. Despite advancements in alternative propulsion technologies, IC engines continue to be a dominant and indispensable power source in many applications.
Challenges and Future Outlook
Discussion on the challenges facing internal combustion engines, such as stricter emissions regulations and the push towards electrification.
Exploration of future trends and innovations, including hybrid powertrains, alternative fuels (biofuels, hydrogen), and advanced engine designs (e.g., opposed-piston engines, variable compression ratio engines).
admin
Related Posts
Aloe Vera- An Insight into its Role in Combating Disease
Aloe Vera- An Insight into its Role in Combating Disease Introduction: Aloe vera often called the “wonder plant” or the “plant of immortality,” it is a kind of succulent plant in the Aloe genus. Originating in the Arabian Peninsula, it
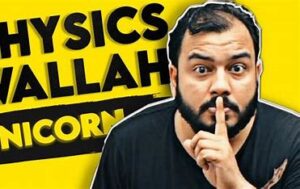
Quality Education For All, Vision of Sustainable Bharat
A Case Study Of Unicorn Physics Wallah INTRODUCTION It was in news everywhere when India overtook the third place with 54 UNICORNS in 2021, this was spread all over the world that India overtook UK to third place in Unicorn
Attracting Families to Your Pharmacy: How to Wow Parents While Wooing Their Little Ones
Pooja Assistant Professor GIP, Geeta University, Panipat In today’s competitive healthcare market, pharmacies must offer more than just convenience and a wide range of products. For many families, the pharmacy is not just a place to pick up medications; it’s