3D PRINTING OF CONCRETE STRUCTURES: REVOLUTIONIZING THE FUTURE OF CONSTRUCTION
Uncategorized3D PRINTING OF CONCRETE STRUCTURES: REVOLUTIONIZING THE FUTURE OF CONSTRUCTION
- August 10, 2024
- Geeta University
Introduction
The construction industry, historically known for its labour-intensive and time-consuming processes, is experiencing a paradigm shift with the advent of 3D printing technology. This technology, also known as additive manufacturing, promises to revolutionize the way we build by offering benefits like reduced construction time, lower costs, enhanced design flexibility, and improved sustainability. This blog explores the technical aspects of 3D printing in construction, delving into its processes, materials, applications, advantages, and challenges, as well as its future potential.
What is 3D Printing in Construction?
3D printing in construction involves the use of specialized printers to create structures layer by layer based on a digital model. This additive manufacturing process differs from traditional subtractive methods, where material is removed from a solid block to create the desired shape. Instead, 3D printing builds the structure by adding material sequentially, reducing waste and allowing for more complex designs. This innovative approach is paving the way for more efficient and versatile construction practices.
How Does 3D Printing of Concrete Work?
The process of 3D printing concrete structures begins with digital modeling, where a 3D model of the structure is created using computer-aided design (CAD) software. This model serves as the blueprint for the printing process, allowing for the creation of intricate geometries that are difficult to achieve with traditional methods. Next, a specially formulated concrete mix is prepared, which must be extrudable through the printer’s nozzle while maintaining structural integrity. This mix often includes additives to enhance properties like workability, setting time, and strength.
During the printing process, the printer follows the digital model’s instructions, depositing concrete layer by layer to build the structure from the ground up. Large-scale printers, which can be gantry-based, robotic-arm-based, or crane-like systems, offer different capabilities in terms of size, speed, and precision. Once printed, the concrete layers begin to cure and harden, achieving the final strength and durability. Additional finishing steps, such as surface smoothing or the integration of reinforcement elements, may be required to complete the structure.
Types of 3D Printing Technologies in Construction
Several 3D printing technologies are employed in construction, each offering unique advantages and limitations. Contour crafting, developed by Dr. Behrokh Khoshnevis, involves extruding concrete in a smooth, continuous process to form vertical walls. This method is efficient for creating large, straight sections of structures like walls and floors. D-shape technology, invented by Enrico Dini, uses a binder jetting method where a binding agent is selectively deposited onto a bed of sand or other granular material, layer by layer, allowing for the creation of free-form and complex geometries.
Concrete printing uses a robotic arm to extrude concrete in layers, offering high flexibility in terms of movement and the ability to create intricate and curved structures. This method is particularly useful for printing customized designs. Selective binding, similar to the D-shape method, uses a binding agent to solidify layers of granular material, providing high precision for detailed structures but is less commonly used in large-scale construction.
Materials Used in 3D Printing of Concrete
The choice of materials is crucial in 3D printing of concrete structures. Ordinary Portland Cement (OPC) is commonly used due to its availability and proven performance, although alternative cements like geopolymers or blended cements offer enhanced properties and sustainability benefits. Fine aggregates, such as sand, are typically used to ensure smooth extrusion and fine layer resolution. The size and gradation of aggregates are essential to prevent nozzle blockages.
Additives and admixtures play a significant role in optimizing the concrete mix for 3D printing. Superplasticizers improve the flowability of the mix without increasing water content, maintaining desired strength and durability. Accelerators speed up the setting time, allowing for faster printing and reduced layer deformation. Reinforcing fibers, such as steel, glass, or polypropylene, enhance tensile strength and crack resistance. The water-to-cement ratio is also a key factor in achieving the right balance between workability and strength, with lower water content improving strength but potentially reducing flowability.
Applications of 3D Printed Concrete Structures
3D printing of concrete is being explored in various construction sectors, offering innovative solutions to traditional challenges. One of the most promising applications is in residential housing, where 3D printing can significantly reduce construction time and costs, making homeownership more accessible. Companies like ICON and Apis Cor have successfully built 3D printed homes in record times, showcasing the potential for rapid, affordable housing solutions.
In the commercial sector, 3D printing is used for constructing office buildings, retail spaces, and warehouses. Large-scale printers can produce entire building components that are assembled on-site, reducing construction timelines and labor costs. For infrastructure projects, 3D printing enables the efficient production of bridges, culverts, and other elements, allowing for complex designs that optimize material usage and structural performance. Notable examples include 3D printed pedestrian bridges in Spain and the Netherlands.
3D printing also offers rapid solutions for disaster relief and emergency shelters. In disaster-stricken areas, this technology can provide quick construction of temporary or permanent shelters, offering immediate relief and long-term housing solutions. Architects and artists are leveraging 3D printing to create unique architectural elements and sculptures, pushing the boundaries of creative expression in construction.
Advantages of 3D Printing in Construction
The adoption of 3D printing technology in construction offers numerous advantages. One of the most significant is the reduction in construction time, as 3D printing automates the building process and eliminates the need for traditional formwork and manual labor. This leads to faster project completion and the potential for continuous operation of the printer, producing components or entire structures more quickly than conventional methods.
Cost savings are another major benefit. Labor costs are reduced as fewer workers are needed, and material waste is minimized due to the precise nature of additive manufacturing. This precision also allows for lower overall costs of building materials, especially when using local or recycled materials. The technology’s flexibility in creating complex geometries and custom designs that are difficult or impossible to achieve with traditional methods also opens new possibilities for innovative architectural solutions.
3D printing contributes to more sustainable construction practices by reducing material waste, energy consumption, and the carbon footprint associated with traditional building methods. The use of alternative materials, such as recycled aggregates or low-carbon cement, further enhances the environmental benefits. Additionally, the ability to produce unique, customized structures meets diverse needs and preferences in residential, commercial, and public projects.
Challenges and Limitations
Despite its many advantages, 3D printing in construction faces several challenges. Ensuring consistent quality and performance of the printed concrete is crucial, as variations in material properties can lead to structural weaknesses or defects. Developing standardized testing and quality control measures is essential to address these concerns. Printed structures must also meet the same safety and durability standards as traditionally constructed buildings, including resistance to loads, weathering, and seismic activity. The lack of established building codes and regulations for 3D printed structures presents a barrier to widespread adoption.
The size of current 3D printers can limit the scale of projects, as large printers are challenging to transport and set up on-site. Advances in printer design and the development of more portable systems are needed to overcome these limitations. Combining 3D printed components with traditional construction methods requires careful planning and coordination to ensure structural integrity and aesthetic coherence. Finally, the initial investment in 3D printing technology can be high, potentially deterring smaller firms or individual builders, and specialized materials used in 3D printing may be more expensive than conventional construction materials.
Innovation and Collaboration
The success and growth of 3D printing in construction depend not only on technological advancements but also on collaboration across various sectors. This includes material scientists, engineers, architects, and policymakers working together to create integrated solutions that address current challenges and future demands. Universities, research institutions, and private companies are partnering to push the boundaries of 3D printing technologies and materials, leading to more efficient and cost-effective methods. These collaborations are crucial for developing novel concrete mixes optimized for printing and exploring new applications.
Establishing guidelines for material quality, structural safety, and environmental impact is essential for ensuring the safety and reliability of 3D printed structures. Regulatory bodies and industry associations are working on creating frameworks that support the acceptance of 3D printing in mainstream construction. Educational institutions are also offering specialized courses and training programs to prepare the next generation of professionals for leveraging this technology effectively. On-site training and workshops help current professionals upgrade their skills and stay abreast of the latest developments.
Real-world applications and successful case studies are critical for demonstrating the viability and benefits of 3D printing in construction. Innovative projects such as ICON’s 3D printed homes in Mexico and the world’s first 3D printed office in Dubai stand as trailblazing examples that encourage and drive wider adoption of 3D printing technology in construction. Industry leaders and early adopters play a vital role in showcasing the capabilities of 3D printing, paving the way for broader acceptance and integration into traditional construction practices.
The Path Forward
Continuous innovation, coupled with strategic partnerships and regulatory support, will drive the technology’s evolution and its integration into mainstream construction. Advancements in materials are focused on developing new concrete formulations with enhanced properties like higher strength, faster curing times, and better sustainability. The use of alternative materials, such as bio-based composites or recycled plastics, is being explored to reduce environmental impact further.
Automation and robotics are expected to improve the precision and efficiency of 3D printing processes. Integration with advanced robotics and automation systems can enhance the flexibility and scalability of construction projects. Hybrid construction methods, combining 3D printing with traditional techniques, offer the best of both worlds by optimizing material usage, reducing costs, and enabling the construction of more complex and robust structures. Large-scale and modular printing innovations aim to increase the size and speed of printing systems, enabling the construction of larger and more complex buildings.
Sustainable and smart construction practices are also a focus, with the integration of sensors and IoT devices into 3D printed structures enhancing functionality and efficiency. Incorporating sustainable practices, including the use of renewable energy sources and recycled materials, reduces the environmental footprint of 3D printing processes. As we look to the future, the promise of faster, cheaper, and more sustainable building methods is within reach, poised to transform how we conceive, design, and construct the built environment.
Bridging the Gap: Integrating 3D Printing with Traditional Construction
The full potential of 3D printing in construction is realized not only through its standalone capabilities but also by its integration with traditional building methods. This hybrid approach harnesses the strengths of both technologies, providing a more versatile and scalable solution to contemporary construction challenges.
Complementary Techniques for Enhanced Construction
Traditional construction methods, such as steel framing, bricklaying, and timber construction, have established themselves as reliable solutions for creating robust, large-scale structures. These techniques excel in providing the necessary load-bearing capacity and stability for high-rise buildings and extensive infrastructure projects. When combined with 3D printing, these conventional methods can be enhanced to offer greater design flexibility and efficiency.
For instance, while traditional methods can be used to construct the primary structural elements like foundations, beams, and columns, 3D printing can be employed to produce intricate and customized components. This could include complex facades, unique interior partitions, or detailed decorative elements that are difficult or costly to achieve using conventional methods. By integrating these approaches, builders can achieve a balance between structural integrity and aesthetic innovation, paving the way for the construction of complex and visually striking buildings.
Streamlining Construction Processes with 3D Printing
Integrating 3D printing into conventional construction workflows can significantly streamline processes and reduce the reliance on manual labor. One practical application is the use of 3D printed molds for concrete casting, which can greatly reduce the time and materials required for creating complex shapes. Traditional concrete formwork is often labor-intensive and wasteful, but 3D printed molds can be customized for each project, allowing for precise and efficient casting.
Moreover, 3D printing can expedite the production of building components that are traditionally prefabricated off-site. For example, precast concrete panels, which are commonly used for walls and flooring, can be 3D printed directly on-site or in a nearby facility, reducing transportation costs and lead times. This approach not only enhances the speed and efficiency of construction projects but also allows for greater flexibility in design modifications during the building process.
The Role of Modular Construction in Hybrid Approaches
Modular construction, where building components are produced in sections off-site and then assembled on-site, can benefit significantly from 3D printing technology. 3D printing enables the production of highly customized modules that can be easily transported and assembled, offering a perfect complement to traditional modular techniques. This synergy allows for the creation of unique architectural designs without the constraints typically associated with on-site construction.
By combining the precision and customization capabilities of 3D printing with the scalability and robustness of traditional construction methods, builders can achieve faster project delivery and improved overall efficiency. This hybrid approach is particularly advantageous for large-scale developments where speed, cost, and design flexibility are critical factors.
Pioneering Projects and the Future of Hybrid Construction
Several pioneering projects around the world illustrate the potential of integrating 3D printing with traditional construction techniques. For example, in the Netherlands, the 3D printed concrete bridge at Gemert showcases how additive manufacturing can complement traditional construction to create functional and aesthetically pleasing infrastructure. Similarly, in Dubai, the 3D printed office building demonstrates how blending new and old methods can lead to innovative architectural solutions that are both practical and forward-thinking.
As the construction industry continues to evolve, the hybridization of 3D printing and traditional methods will play a crucial role in shaping the future of building. This integrated approach not only leverages the best of both worlds but also opens up new possibilities for sustainable, efficient, and creative construction. With ongoing advancements in technology and materials, the synergy between 3D printing and conventional construction practices promises to redefine how we build in the years to come.
Conclusion
3D printing of concrete structures represents a transformative shift in the construction industry. With its potential to revolutionize building methods, this technology offers unprecedented opportunities for innovation, efficiency, and sustainability. As research and development continue to advance, 3D printing is poised to play a pivotal role in shaping the future of construction. From creating affordable housing and intricate architectural designs to robust infrastructure, 3D printing is unlocking new possibilities and transforming the built environment. The journey of integrating this cutting-edge technology into mainstream construction practices is just beginning, and its impact is bound to be profound and far-reaching.
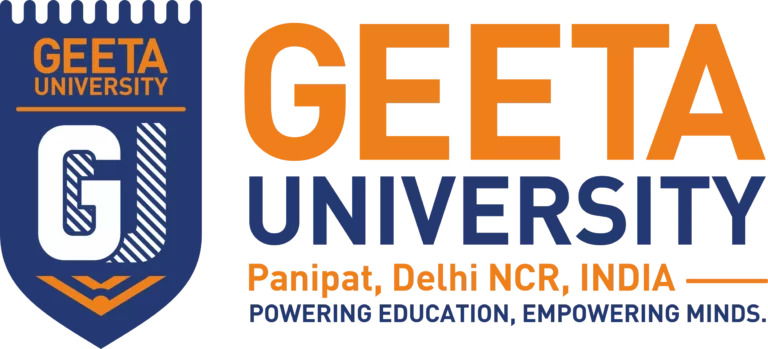
Admission Open 2024-2025
For Your bright Future
Tags
Related Posts
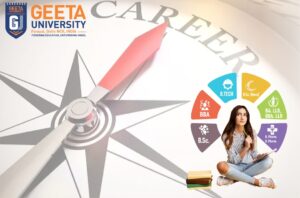
Why career guidance is important after 10th and 12th class – Geeta University
More than 95% students pass their class 10th and 12th Board examination, but how many of them make an effective choice post the completion of their respective educational milestones. It is rather significant to be mindful of the choices you
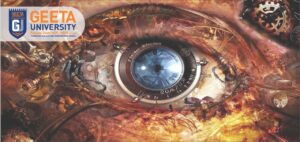
Best Courses After 12th Commerce, Future, Scope and Career Prospects – Geeta University
If you do Mathematics as an additional subject in classes 11 and 12, you are eligible for many courses as a second-degree qualified student. All of these subjects validate the need for Mathematics as a subject. In this competitive world,
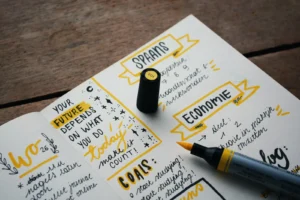
Diploma Courses in Engineering After Class 10th – Geeta University
Do you enjoy creating, designing, constructing, and maintaining tools and machines? If so, engineering is the ideal career for you. For those who desire to pursue technical education while also beginning their careers early, a diploma in engineering is a