The Ultimate Guide to Concrete: Past, Present, and Future.
UncategorizedThe Ultimate Guide to Concrete: Past, Present, and Future
- January 9, 2025
- Geeta University
Mr.Rohit Biddu
A Brief History of Concrete
From ancient Egypt to modern skyscrapers, it has been the backbone of architectural advancement.
Ancient Uses of Concrete
- Egyptians (circa 3000 BC): The earliest forms of concrete were used in the pyramids. They combined mud with straw and sometimes gypsum or lime to create durable structures.
- Romans (circa 200 BC – 400 AD): The Romans mastered the art of concrete. Roman concrete, or opus caementicium, was made with volcanic ash, lime, and water, resulting in structures like the Pantheon and aqueducts that have stood the test of time.
Concrete in the Modern Era
- 1824: The invention of Portland cement by Joseph Aspdin revolutionized concrete production, making it more durable and versatile.
- 20th Century: Innovations like reinforced concrete and precast concrete enabled skyscrapers, bridges, and modern transportation systems.
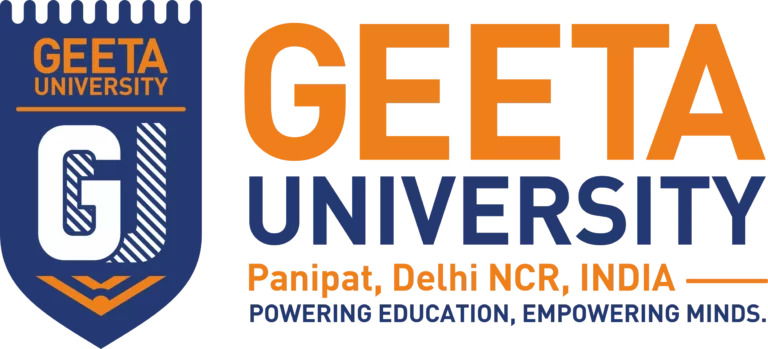
Admission Open 2024-2025
For Your bright Future
The Composition of Concrete
Concrete is a composite material composed of:
- Cement: The binding agent, usually Portland cement.
- Types of Concrete
High-Strength Concrete
- Designed for projects requiring exceptional durability, such as bridges and high-rise buildings.
Lightweight Concrete
- Incorporates lightweight aggregates like expanded clay, reducing weight without compromising strength.
Self-Healing Concrete
- Embedded with bacteria that produce limestone to seal cracks, extending the material’s lifespan.
Green Concrete
- Made with sustainable materials like fly ash or recycled aggregates, reducing the carbon footprint.
- Applications of Concrete
Residential Construction
- Foundations and Basements: Essential for stability and durability.
- Driveways and Patios: Withstanding weather and wear.
Commercial and Industrial Buildings
- High-Rise Structures: Concrete’s compressive strength makes it ideal for skyscrapers.
Infrastructure
- Bridges and Roads: Reinforced concrete ensures longevity and load-bearing capacity.
- Dams and Water Systems: Impermeability makes it excellent for water containment.
Decorative Applications
- Polished concrete floors, stamped concrete patios, and custom architectural designs.
- Advantages of Concrete
Concrete’s popularity stems from its many advantages:
- Durability: Withstands weather, wear, and time.
- Versatility: Adaptable to various shapes and uses.
- Cost-Effective: Abundant raw materials keep costs low.
- Thermal Mass: Stores heat effectively, enhancing energy efficiency.
- Sustainability: Innovations like green concrete reduce environmental impact.
- Challenges and Limitations
Despite its benefits, concrete has challenges:
- Environmental Impact: Cement production contributes to 8% of global CO2 emissions.
- Brittle Nature: While strong in compression, concrete is weak in tension, requiring reinforcement.
- Cracking: Thermal expansion and shrinkage can lead to cracks, compromising durability.
- Lifespan Limitations: Requires maintenance and can deteriorate over time due to corrosion or freeze-thaw cycles.
- Innovations in Concrete Technology
Carbon Capture in Cement
- New processes capture CO2 during cement production, significantly reducing emissions.
Recycled Concrete Aggregates
- Using crushed concrete from demolished structures as aggregates in new concrete.
3D-Printed Concrete
- Allows for complex shapes and faster construction, revolutionizing the industry.
Transparent Concrete
- Embedded optical fibers create a translucent effect, merging aesthetics and functionality.
Smart Concrete
- Embedded sensors monitor structural health, detecting cracks or stress in real time.
- Sustainability in Concrete Production
The concrete industry is embracing sustainability:
- Supplementary Cementitious Materials (SCMs): Substitutes like fly ash or slag reduce reliance on Portland cement.
- Recycled Water: Used in the mixing process to conserve fresh water.
- Energy-Efficient Kilns: Reducing fuel consumption during cement production.
- The Future of Concrete
Concrete continues to evolve, with exciting developments on the horizon:
- Ultra-High-Performance Concrete (UHPC): Combining extreme strength with ductility for innovative designs.
- Self-Healing Concrete: Prolonging lifespan and reducing maintenance costs.
- Bio-Concrete: Harnessing microbial action to produce eco-friendly alternatives.
- Final Thoughts
While challenges like environmental impact remain, advancements in technology and sustainable practices are paving the way for a greener, more innovative future. By understanding its history, composition, and applications, we can better appreciate the material that shapes our lives.
Special Types of Concrete
- High-Performance Concrete (HPC)
- Definition: Concrete with superior strength, durability, and workability, designed for specific structural or environmental challenges.
- Applications: Bridges, tall buildings, and structures exposed to harsh weather or chemicals.
- Self-Healing Concrete
- Definition: Concrete that autonomously repairs cracks using embedded agents like bacteria or polymers.
- Mechanism: Bacteria produce limestone when exposed to water, sealing cracks.
- Applications: Long-lasting infrastructure like bridges, tunnels, and water systems.
- Advantages: Reduces maintenance and increases lifespan.
- Fiber-Reinforced Concrete (FRC)
- Definition: Concrete reinforced with fibers (steel, glass, synthetic, or natural) to improve tensile strength.
- Applications: Pavements, industrial floors, and structures prone to cracking.
- Advantages: Enhanced ductility, reduced cracking, and improved impact resistance.
- Lightweight Concrete
- Applications: Non-load-bearing walls, insulation layers, and lightweight structures.
- Ultra-High-Performance Concrete (UHPC)
- Definition: A blend of fine materials and steel fibers that produces exceptionally strong and durable concrete.
- Applications: Bridges, military structures, and architectural elements.
- Advantages: High compressive strength, ductility, and resistance to wear and corrosion.
- Decorative Concrete
- Definition: Concrete designed for aesthetic purposes, such as polished, stamped, or colored finishes.
- Applications: Driveways, patios, floors, and countertops.
- Advantages: Customizable, visually appealing, and durable.
- Transparent Concrete
- Definition: Concrete embedded with optical fibers to allow light to pass through.
- Applications: Architectural facades, interior partitions, and lighting features.
- Roller-Compacted Concrete (RCC)
- Definition: A dry mix with minimal water, compacted using heavy machinery.
- Applications: Dams, pavements, and industrial floors.
- Advantages: Cost-effective, durable, and fast to apply.
- Shotcrete
- Applications: Tunnel linings, slope stabilization, and repair works.
- High-Density Concrete
- Definition: Made with heavy aggregates like barite to achieve high density.
- Applications: Radiation shielding in nuclear plants and X-ray rooms.
- Advantages: Excellent shielding properties and durability.
- Pervious Concrete
- Applications: Stormwater management systems, driveways, and pedestrian paths.
- Advantages: Reduces water runoff and replenishes groundwater.
- Precast Concrete
- Definition: Concrete elements cast and cured in a controlled environment, then transported to the site.
- Applications: Beams, panels, and modular components.
- Advantages: High-quality finish, reduced on-site labor, and faster construction.
- Refractory Concrete
- Applications: Furnaces, kilns, and chimneys.
- Advantages: Withstands extreme temperatures and thermal cycling.
- Polymer Concrete
- Applications: Acid-resistant tanks, drainage channels, and industrial flooring.
- Advantages: High strength, corrosion resistance, and fast curing.
Testing of Concrete: Ensuring Strength, Durability, and Safety
Concrete is a cornerstone of modern construction, used in everything from residential buildings to massive infrastructure projects. Ensuring its quality is vital for safety, durability, and performance. Testing concrete involves evaluating its properties at different stages, from raw material to hardened structure. This article explores the various tests conducted on concrete, their significance, and the methods used.
- Importance of Concrete Testing
Concrete testing is critical for the following reasons:
- Ensuring Strength and Durability: It confirms the concrete meets design specifications and will endure environmental stresses.
- Compliance with Standards: Ensures adherence to codes like ASTM, IS, or BS standards.
- Cost Optimization: Reduces wastage and prevents overuse of materials.
- Predicting Performance: Provides insights into how the structure will behave under different conditions.
- Quality Assurance: Ensures consistency in concrete production.
- Categories of Concrete Tests
Concrete tests can be broadly classified into:
- Fresh Concrete Tests: Assess the quality and workability of concrete before it sets.
- Hardened Concrete Tests: Evaluate strength, durability, and performance after curing.
- Destructive and Non-Destructive Tests: Depending on whether the test damages the structure or leaves it intact.
- Tests on Fresh Concrete
3.1 Slump Test
- Purpose: Measures workability and consistency.
- Types of Slump:
- True Slump: Uniform reduction in height.
- Shear Slump: Concrete slides sideways.
- Collapse Slump: Complete disintegration.
- Applications: Used at construction sites for quick quality checks.
3.2 Air Content Test
- Importance: Vital for freeze-thaw resistance in colder climates.
3.3 Compaction Factor Test
- Purpose: Determines workability, especially for low-slump concrete.
- Procedure:
- Measure the weight of partially and fully compacted concrete.
- Calculate the compaction factor as the ratio of the two weights.
3.4 Temperature Test
- Purpose: Ensures the concrete temperature is within permissible limits.
- Importance: Helps in managing hydration and setting time, especially in extreme weather.
- Tests on Hardened Concrete
4.1 Compressive Strength Test
- Procedure:
- Prepare standard cube or cylindrical samples.
- Cure them in water for 7, 14, or 28 days.
- Test under a compression testing machine.
- Significance: Determines the grade and suitability of concrete for structural applications.
4.2 Split Tensile Strength Test
- Purpose: Evaluates tensile strength, an area where concrete is weak.
4.3 Flexural Strength Test
- Procedure:
Place a beam specimen on supports.
- Importance: Relevant for pavement and slab design.
4.4 Modulus of Elasticity Test
- Purpose: Determines the deformation characteristics under stress.
- Applications: Important for high-rise structures and seismic design.
- Non-Destructive Tests
5.1 Rebound Hammer Test
- Purpose: Estimates surface hardness and compressive strength.
- Method: A spring-controlled hammer strikes the surface, and the rebound distance is measured.
- Advantages: Quick and does not damage the structure.
5.2 Ultrasonic Pulse Velocity (UPV) Test
- Purpose: Detects cracks, voids, and uniformity in concrete.
- Procedure:
- Send ultrasonic pulses through the concrete.
- Applications: Used for quality assurance and assessing the integrity of old structures.
5.3 Penetration Resistance Test
- Purpose: Measures surface strength by driving a steel rod into the concrete.
- Significance: Indicates compressive strength without coring.
5.4 Ground Penetrating Radar (GPR)
- Purpose: Maps internal features, such as reinforcement placement or voids.
- Applications: Useful for locating utilities and assessing historical structures.
- Specialized Tests
6.1 Permeability Test
- Purpose: Assesses water penetration and durability.
- Procedure: Measure water flow through a concrete sample under pressure.
- Importance: Relevant for dams, water tanks, and marine structures.
6.2 Chloride Penetration Test
- Purpose: Determines resistance to chloride ingress.
- Method: Measure chloride ion diffusion through a concrete sample.
- Applications: Critical for structures exposed to seawater or de-icing salts.
6.3 Carbonation Test
- Purpose: Evaluates the depth of carbonation, which can lead to steel corrosion.
- Procedure: Spray phenolphthalein on a concrete surface and observe color changes.
- Importance: Ensures longevity in reinforced structures.
6.4 Thermal Conductivity Test
- Purpose: Measures the heat transfer properties of concrete.
- Applications: Used in energy-efficient building designs.
- Factors Influencing Test Results
Several factors can impact the results of concrete tests:
- Mix Design: Cement-to-water ratio, type of aggregates, and admixtures.
- Curing Conditions: Temperature, humidity, and duration.
- Sample Preparation: Accurate molding and compaction.
- Testing Equipment: Calibration and maintenance of machines.
Interpreting Test Results
Concrete testing results must be analyzed carefully:
- Compare values against specified standards (e.g., compressive strength ≥ 25 MPa for M25 concrete).
- Assess uniformity across multiple samples.
Challenges in Concrete Testing
- Variability in Results: Due to environmental conditions and human error.
- Non-Standard Practices: Using uncalibrated equipment or improper sampling.
Conclusion
Testing concrete is indispensable for ensuring its quality and reliability in construction projects. From assessing workability in fresh concrete to determining strength in hardened concrete, each test serves a specific purpose. Innovations in testing methods, such as non-destructive techniques, continue to improve efficiency and accuracy. By adhering to standardized practices, engineers can guarantee the safety, performance, and longevity of concrete structures.
- Definition of Workability
Workability can be understood as the combination of properties that govern the ease of placement and the homogeneity of concrete. High workability means the concrete can flow into complex shapes and compact easily, while low workability may lead to difficulty in handling and uneven distribution of aggregates.
- Importance of Workability
The importance of workability lies in its influence on various stages of concrete use:
- Mixing and Transportation: Ensures proper blending of materials and ease of transport to the site.
- Placing and Compacting: Facilitates filling molds and eliminating air voids, ensuring density and strength.
- Finishing: Enables smooth surface finishing for aesthetics and functionality.
- Factors Affecting Workability
Several factors influence the workability of concrete:
3.1 Water-Cement Ratio
- Higher Ratio: Increases workability as water acts as a lubricant.
- Lower Ratio: Reduces workability but improves strength.
3.2 Aggregate Properties
- Size: Larger aggregates reduce workability due to less surface area.
- Shape: Rounded aggregates improve workability, while angular ones decrease it.
- Grading: Well-graded aggregates enhance workability by reducing voids.
3.3 Admixtures
- Plasticizers: Improve flowability without increasing water content.
- Superplasticizers: Provide high workability for complex structures or dense reinforcement.
3.4 Cement Content
- Higher cement content increases workability by providing more paste for lubrication.
- Measurement of Workability
Workability is measured using various tests to suit the project requirements and concrete type:
4.1 Slump Test
- Results Interpretation:
- High Slump (150-175 mm): High workability, suitable for pumped concrete.
- Medium Slump (50-100 mm): Moderate workability, ideal for beams and slabs.
- Low Slump (<50 mm): Low workability, used for foundations and road pavements.
4.2 Compaction Factor Test
- Purpose: Measures the degree of compaction achieved by a standard weight.
- Procedure: Concrete is placed in two hoppers and compacted; the ratio of weights (compacted to uncompacted) determines the factor.
- Types of Concrete Workability
Concrete can exhibit different levels of workability based on its mix design and intended use:
- Very Low Workability: Used for mass concreting (e.g., dams).
- Low Workability: Suitable for pavements and foundations.
- Medium Workability: Ideal for slabs, beams, and columns.
- High Workability: Required for thin sections or heavily reinforced structures.
Conclusion
Workability is a vital property of concrete that determines its performance from mixing to hardening. By understanding and controlling factors like water-cement ratio, aggregates, and admixtures, engineers can achieve the desired workability for specific applications. Regular testing ensures consistent quality, helping to create durable and reliable structures.
Tags
Related Posts
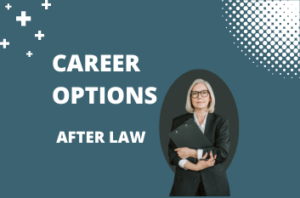
What Are the Career Options for A Law Graduate In India – Geeta University
The legal profession in India has undergone numerous changes over the years. Lawyers are no longer confined to the courtroom where they represent their clients. Law graduates today work in a variety of settings, including corporations, IT firms, administrative services,
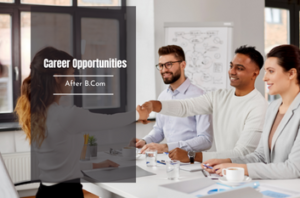
What to do After B.Com.? Career Opportunities After B.Com. – Geeta University
When choosing which course to pursue, the main factor one keeps in mind is one’s future career and its scope. There are various preferred and popular courses that individuals choose as bachelors, one such popular course is B Com (Bachelor
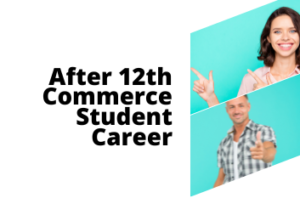
Career Options for Commerce Students After 12th – Geeta University
After completing your 12th board, you must have been confused or worried about what course you want to pursue to achieve your career in commerce and from where you can complete your higher studies. Not how clearly you are Career