INTRODUCTION TO ALUMININUM ALLOY
EngineeringINTRODUCTION TO ALUMININUM ALLOY
- January 9, 2025
- Geeta University
Heading
Aluminium is the second most plentiful element on the planet. It is a lightweight and soft metal, which is recognized in dull appearance with silvery white colour. Aluminium offers high strength in its alloy forms even it is three times lighter than the steel. Aluminium is at second number in the list of malleable materials and at sixth position in ductility. Due to
these characteristics aluminium has become one of the most important materials in the 20th
century. Aluminium has a face-centered (FCC) structure which makes it easy to produce its components and fabricated at comparatively lower cost. Pure aluminium has low density (2.7 gm/cm2), lower melting temperature (660oC) and low tensile strength (40-50 MPa) in the annealed condition. Different heat treatments, cold working and alloying processes are used to strengthen it. Formability, strength, thermal conductivity and corrosion resistance are improved by making aluminium alloys with numerous elements. These alloys provide a broad range of potential and applicability that makes this material most in demand in the manufacturing sector, automobile sector, aeronautical sector, shipbuilding, transport sector, railway sector, fabrication and buildings
1000 series: (Non Heat Treatable)
This series restricted for 99% of aluminium composition so it is referred as pure aluminium series. Alloys of this series have poor mechanical properties (ultimate tensile strength 70 –
185 MPa) so it would seldom be used for structure applications only. But these alloys are primarily used for chemical tanks and pipes in the chemical industry due to their superior resistance against corrosion. Due to greater electrical properties (brilliant electrical conductivity), these are also recommended for application in the bus bar.
2000 series: (Heat treatable)
The main alloying element of this alloy series is copper (0.7-6.8 wt %) which makes it high strength and high-performance alloy series and have applications in aircraft and aerospace industry. These alloys have excellent mechanical strength even at elevated temperature. 2000 series alloys preferably considered as non-weldable alloy due to the risk of thermal cracking and stress corrosion cracking.
3000 series: (non – heat treatable)
Manganese is the main alloying element for this series with allowable wt% from 0.05 to
1.8%. These alloys are fit to use at elevated temperature with moderate mechanical strength, good corrosion strength and good formability. Pots and pans are generally made of alloys of this series. But in recent scenario, these alloys are the first choice to manufacture of heat exchanger in power plants and vehicles. The moderate strength of these alloys increases the application in the area of structural fabrication also.
4000 series: (Heat treatable and non-heat treatable)
Silicon is added as the main constituents in the aluminium for this series of alloys from 0.6 to
21.5 wt %. This is only the series of aluminium alloys which contains both heat treatable as well as non-heat treatable alloys as well. Addition of silicon in aluminium reduces the melting temperature and improves the flowability in a molten state. The low melting point and good flowability provide the applicability as the filler material in welding and brazing.
The problem associated with the welding of aluminium alloys is due to the melting and recasting of the material in weld zone. High temperature also cause unwanted grain growth in HAZ. Solution to these problems is to produce the weld at a temperature lower than the melting point of the aluminium. Researchers and designers have developed some welding methods such as resistance welding, thermit welding, pressure welding, friction welding etc. However, friction stir welding (FSW) which is invented in 1991 by The Institute of Welding (TWI) in Britain proved to be the most significant welding process for aluminium alloys.
5000 series: (non-heat treatable)
Magnesium is the major alloying element for this series of aluminium alloys with the allowable wt% from 0.2 to 6.2%. This series has maximum mechanical strength among other non-heat treatable series of alloys. The strength and weldability provide this series a wide variety of applications such as ship-building, bridges building, transportation and pressure vessels etc. Generally, these alloys are not suggested for use at superior temperature due to susceptibility to thermal cracking.
6000 series: (heat treatable)
Magnesium and silicon are added (around 1% of wt %) to aluminium to develop this series of alloys. Presence of magnesium and silicon makes a magnesium-silicide compound to provide improved mechanical strength through solution heat treatment. Alloys of this series are commonly in form of extrusion and have application in the area of many structural components.
7000 series: (heat treatable)
The main alloying element of this series is zinc with allowable wt% of 0.8 to 12 %. This series of alloys comprises the highest mechanical strength among all aluminium alloys. Due to their mechanical strength, these are used as high-performance application materials in aircraft, aerospace, railways, transportation vehicles etc
.
Welding is an essential process in industries ranging from construction and automotive to aerospace and manufacturing . Fusion welding was generally used to weld the aluminium and its alloys in early stages of use of aluminium alloy in industries. The melting of material from the edges to be weld due to heat input by the heat source and then solid recasting of the same material produce the weld joint. But High thermal conductivity, shrinkage during solidification, high thermal expansion and high hydrogen solubility in the molten state make the welding of aluminium alloys challenge for designer and researcher. The above-said properties of aluminium leads to the less fusion due to a layer of oxides, the inclusion of slag, partial penetration, thermal cracks, hot tears, undercut and porosity in the welds. Gas tungsten inert welding (TIG).
Welding defects:-
- Surface Defects: Visible to the naked eye, these defects occur on the surface of the weld. Examples include cracks, porosity, and undercuts.
- Internal Defects: These are hidden within the weld and require advanced techniques such as ultrasonic testing or radiographic examination to detect. Common examples include slag inclusions, lack of fusion, and incomplete penetration.
- Description: Gas pockets or voids trapped within the weld.
- Causes:
- Contaminants such as oil, rust, or moisture on the welding surface.
- Incorrect shielding gas flow.
- Improper electrode handling.
- Impact: Reduces weld strength and can lead to failure under stress.
- Cracking
Fractures in the weld or surrounding base metal.
- Types:
- Hot cracking (occurs during solidification).
- Cold cracking (occurs after cooling).
- Causes:
- Excessive stress.
- Poor material selection.
- Rapid cooling rates.
- Impact: Compromises structural integrity.
- Types:
- Lack of Fusion
- Description: The weld metal fails to fuse with the base material or preceding weld layers.
- Causes:
- Insufficient heat input.
- Incorrect welding angle or speed.
- Presence of oxides or other contaminants.
- Impact: Weak weld joint, leading to premature failure.
- Incomplete Penetration
- Description: The weld does not fully penetrate the joint thickness.
- Causes:
- Low heat input.
- Improper joint preparation.
- Incorrect electrode size or technique.
- Impact: Weak joints that may fail under load.
- Undercut
- Description: A groove melted into the base material adjacent to the weld.
- Causes:
- Excessive welding speed.
- Incorrect electrode angle.
- High current settings.
- Impact: Reduces the cross-sectional area of the base metal, weakening the structure.
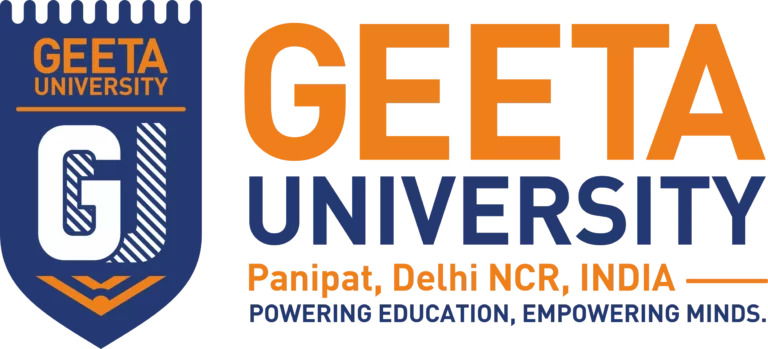
Admission Open 2024-2025
For Your bright Future
Advanced Detection Techniques for Welding Defects
Modern welding processes require advanced inspection methods to ensure defect-free welds. Here are some state-of-the-art techniques:
- Ultrasonic Testing (UT)
- High-frequency sound waves are used to detect internal defects.
- Advantages: Precise, non-destructive, and suitable for various materials.
- Radiographic Testing (RT)
- X-rays or gamma rays penetrate the weld to reveal internal defects.
- Advantages: Detailed imaging of weld flaws.
- Eddy Current Testing
- Electromagnetic induction detects surface and near-surface defects.
- Advantages: Fast and non-destructive.
- Magnetic Particle Testing (MPT)
- Magnetic fields reveal surface and slightly subsurface cracks.
- Advantages: Simple and effective for ferromagnetic materials.
- Dye Penetrant Testing
- A dye highlights surface defects through capillary action.
- Advantages: Cost-effective and easy to implement.
- Phased Array Ultrasonic Testing (PAUT)
- Advanced UT technique offering detailed 3D imaging of welds.
Advantages: High accuracy and adaptability
Advanced Welding Technologies to Mitigate Defects
- Laser Beam Welding (LBW)
- Offers high precision, minimal distortion, and deep penetration.
- Ideal for complex geometries and high-strength materials.
- Friction Stir Welding (FSW)
- A solid-state process that reduces porosity and cracking risks.
- Suitable for lightweight alloys like aluminum.
- Hybrid Welding Techniques
- Combines processes like laser and arc welding for superior results.
- Balances speed, strength, and precision.
- Cold Metal Transfer (CMT)
- A low-heat process that minimizes spatter and thermal distortion.
- Excellent for thin materials and dissimilar metal joints.
- Additive Manufacturing with Welding
- Layer-by-layer deposition for custom components.
- Reduces waste and enables complex designs.
Repair and Remediation of Welding Defects
Despite preventive measures, defects may still occur. Advanced repair techniques include:
- Grinding and Rewelding
- Removes surface defects and prepares for re-welding.
- Thermal Stress Relief
- Reduces residual stresses to prevent cracking.
- Post-Weld Heat Treatment (PWHT)
- Enhances weld properties and reduces defects.
- Weld Overlay
- Adds material layers to compensate for defects or wear.
Conclusion
Welding defects can significantly impact the performance and safety of structures. Advanced technologies and strategies have made it possible to detect, prevent, and repair these defects more effectively. By integrating proper material handling, optimized techniques, and cutting-edge inspection methods, industries can achieve defect-free welds and enhance the reliability of their products.
Investing in advanced welding solutions not only ensures compliance with quality standards but also minimizes costs associated with repairs and downtime. As welding technology continues to evolve, embracing these innovations will remain key to overcoming challenges and achieving excellence in the field.
Taguchi method is utilized for control of quality, loss function of quality, design of parameters, design of tolerance, and design of experiments with the help of orthogonal arrays (OA). There are two aspects of Taguchi‟s philosophy, first the conceptual structure for the planning of experiments for design of process and product, second the collection of the information by specific methods and procedures. Taguchi suggested orthogonal arrays for the planning of the experiments which are the Garaeco-Latin squares generalized forms. An appropriate orthogonal array is selected for design of experiments for given number of process parameters and their interactions
Equipment Used in Gas Welding:-
- Oxygen Gas Cylinder: Contains oxygen at a high pressure, essential for combustion.
- Fuel Gas Cylinder: Commonly contains acetylene, propane, or hydrogen.
- Regulators
- Control the pressure of gases delivered from the cylinders to the torch.
- Welding Torch
- Mixes oxygen and fuel gas in controlled proportions and directs the flame.
- Hoses
- Flexible tubes that transport gases from cylinders to the torch.
- Filler Rods
- Additional material used to strengthen the weld.
- Flame Arrestors
- Prevent the reverse flow of gases, ensuring safety.
- Protective Equipment
- Includes goggles, gloves, and flame-resistant clothing for welder protection.
- The Gas Welding Process
- Setup
- Secure gas cylinders in a vertical position.
- Attach hoses, regulators, and the torch securely.
- Flame Adjustment
- Open oxygen and fuel gas valves slightly.
- Ignite the fuel gas and adjust the flame to achieve the desired type:
- Neutral Flame: Equal oxygen and fuel gas; ideal for welding.
- Oxidizing Flame: Excess oxygen; used for specific metals.
- Carburizing Flame: Excess fuel gas; used for surface hardening.
- Protective Equipment
- Includes goggles, gloves, and flame-resistant clothing for welder protection.
- The Gas Welding Process
- Setup
- Secure gas cylinders in a vertical position.
- Attach hoses, regulators, and the torch securely.
- Flame Adjustment
- Open oxygen and fuel gas valves slightly.
- Ignite the fuel gas and adjust the flame to achieve the desired type:
- Neutral Flame: Equal oxygen and fuel gas; ideal for welding.
- Oxidizing Flame: Excess oxygen; used for specific metals.
Carburizing Flame: Excess fuel gas; used for surface hardening.
Tags
Related Posts
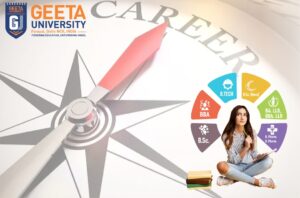
How to find the correct stream after the 10th standard? – Geeta University
Are you confused about which stream to choose after 10th? What is the best stream of the future? What should you learn after Class 10th? Almost all students sails in the same boat. These are the top questions asked by
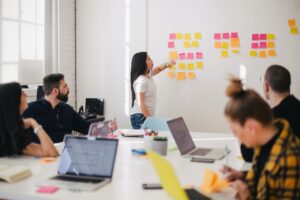
Best Courses After 12th Science, Future, Scope and Career Prospects – Geeta University
One question that keeps popping up in the minds of all 12th grade students is how to choose a safe, secure and fruitful career option. The task of choosing the right path can be difficult for Grade 12th students specially
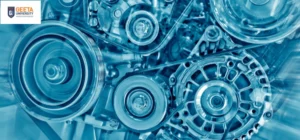
Best Courses After 12th Arts, Future, Scope and Career Prospects – Geeta University
It is important to choose the right subject for your graduation because it is probably the most important time for your study. Making the right decision today will put you on the path to school and professional success by enrolling