4D Printing
Engineering4D Printing
- January 9, 2025
- Geeta University
Introduction
4D printing refers to the fabrication of materials or structures that can change their configuration over time. The “fourth dimension” in this context is time, emphasizing the dynamic nature of the printed objects. This technology relies on smart materials like shape-memory polymers, hydrogels, and other programmable materials that react predictably to external stimuli.
Key Components of 4D Printing:
- Smart Materials: The core enablers of 4D printing are materials engineered to exhibit specific responses. For instance, shape-memory alloys can return to a predefined shape when exposed to heat.
- Stimuli-Responsive Behaviors: External triggers such as temperature changes, pH levels, or electromagnetic fields initiate the transformation of the printed structure.
- Design Algorithms: Computational models are crucial for predicting and designing the behavior of 4D-printed objects under various conditions.
- Additive Manufacturing Techniques: Advanced 3D printing technologies, including stereolithography (SLA) and fused deposition modeling (FDM), are adapted to handle smart materials effectively.
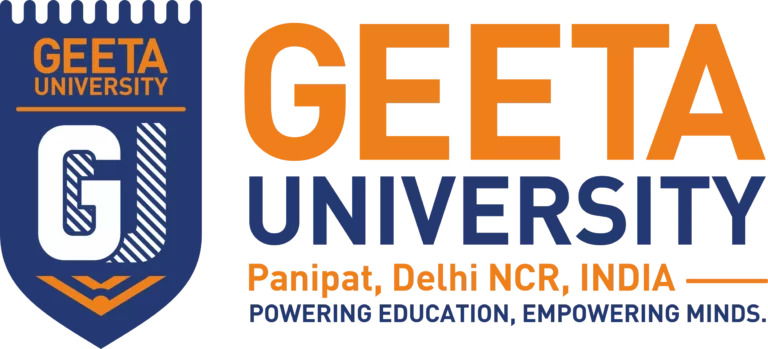
Admission Open 2024-2025
For Your bright Future
Principles of 4D Printing in Mechanical Engineering
The implementation of 4D printing in mechanical engineering hinges on several foundational principles:
- Programming Material Behavior:
- Mechanical engineers use computational tools to program the behavior of smart materials. For example, finite element analysis (FEA) can simulate how a 4D-printed structure will respond to environmental changes.
- Design for Multifunctionality:
- Engineers aim to design components that perform multiple functions. A single 4D-printed part might act as a sensor, actuator, and load-bearing structure simultaneously.
- Customization and Precision:
- Tailoring materials and designs to specific applications is central to 4D printing. This precision ensures optimal performance in demanding environments.
- Scalability:
Developing scalable processes is essential for the widespread adoption of 4D printing in industrial applications.
Applications of 4D Printing in Mechanical Engineering
- Aerospace and Automotive Industries
- Self-Healing Components: Smart materials in 4D-printed parts can repair minor damages autonomously, reducing maintenance costs and increasing durability.
- Shape-Morphing Aerodynamic Surfaces: Aircraft wings or automotive components can change shape in response to varying aerodynamic conditions, improving fuel efficiency.
- Biomedical Devices
- Dynamic Implants: 4D-printed implants can adapt to a patient’s anatomy or deliver drugs in a controlled manner.
- Stents and Catheters: These medical devices can expand or contract in response to body temperature or pH levels, enhancing their functionality.
- Energy Systems
- Solar Panels: 4D-printed materials can optimize the orientation of solar panels based on the sun’s position, maximizing energy capture.
- Pipelines: Smart pipelines can adapt to environmental conditions, reducing the risk of leaks or damage.
- Robotics
- Soft Robotics: 4D printing enables the fabrication of soft, flexible robots that can navigate complex environments and perform delicate tasks.
- Self-Assembly Mechanisms: Components that assemble themselves upon reaching their destination could simplify robotic manufacturing processes.
- Infrastructure and Construction
- Adaptive Structures: Buildings or bridges made with 4D-printed materials can respond to environmental stresses such as wind or earthquakes, enhancing safety and resilience.
Advantages of 4D Printing
- Increased Efficiency:
- 4D printing reduces the need for complex assemblies by integrating multiple functionalities into a single part.
- Cost Savings:
- Self-healing and adaptive materials can extend the lifespan of components, lowering maintenance and replacement costs.
- Sustainability:
- The use of programmable materials reduces material waste and promotes energy efficiency.
- Customization:
- Components can be tailored to specific needs, offering unparalleled levels of customization.
Challenges in 4D Printing
- Material Limitations:
- Developing materials with reliable and predictable responses to stimuli remains a significant challenge.
- Complexity in Design:
- Designing components that integrate multiple functionalities and respond dynamically to stimuli requires advanced computational tools and expertise.
- High Costs:
- The initial costs of smart materials and advanced printing systems can be prohibitive for small-scale applications.
- Scalability Issues:
- Adapting 4D printing for mass production without compromising quality is an ongoing challenge.
- Lack of Standardization:
- Industry-wide standards for 4D printing processes and materials are still under development.
Future of 4D Printing in Mechanical Engineering
The potential of 4D printing in mechanical engineering is vast and largely untapped. Several trends and advancements indicate a promising future for this technology:
- Integration with Artificial Intelligence (AI):
- AI algorithms can enhance the design process, enabling faster and more efficient programming of smart materials.
- Advances in Material Science:
- The development of more robust and versatile smart materials will broaden the applications of 4D printing.
- Sustainable Manufacturing:
- 4D printing can contribute to eco-friendly manufacturing processes by reducing material usage and energy consumption.
- Collaborative Research:
- Partnerships between academia, industry, and government organizations will accelerate the development and adoption of 4D printing technologies.
- Education and Training:
- Incorporating 4D printing concepts into engineering curricula will prepare the next generation of engineers to leverage this technology effectively.
Conclusion
4D printing represents a paradigm shift in manufacturing, offering transformative possibilities for mechanical engineering. By leveraging smart materials and advanced design algorithms, engineers can create adaptive, multifunctional components that redefine traditional manufacturing paradigms. While challenges remain, ongoing research and development are steadily overcoming these barriers, paving the way for 4D printing to become a cornerstone of modern engineering.
As industries strive for greater efficiency, sustainability, and innovation, 4D printing stands as a beacon of what’s possible when technology and creativity converge. Mechanical engineers, poised at the forefront of this revolution, have the opportunity to harness 4D printing to shape a smarter, more responsive, and sustainable future.
Introduction
3D printing, also known as additive manufacturing, has undergone remarkable advancements since its inception in the 1980s. Originally a tool for prototyping, 3D printing has evolved into a versatile technology with applications across industries, including healthcare, aerospace, automotive, and construction. Today, the convergence of material science, engineering, and digital design has propelled 3D printing to the forefront of innovation, enabling the creation of complex, customized, and functional components at an unprecedented scale.
The Evolution of 3D Printing Technologies
The growth of 3D printing can be attributed to continuous advancements in printing technologies, materials, and processes. Below are some notable innovations:
- Multi-Material Printing
- Description: Modern 3D printers can now integrate multiple materials into a single print, allowing the creation of parts with varied properties, such as stiffness, elasticity, or conductivity.
- Applications: Multi-material printing is widely used in creating prosthetics, electronic components, and aerospace parts.
- High-Speed Printing
- Description: New techniques such as Continuous Liquid Interface Production (CLIP) and Multi Jet Fusion (MJF) have drastically increased printing speeds.
- Applications: High-speed printing enables faster production of prototypes and functional parts, making 3D printing more viable for mass production.
- Large-Scale 3D Printing
- Description: Advances in printer size and scalability now allow for the fabrication of large components, such as car bodies and architectural structures.
- Applications: This is particularly transformative for the construction industry, where entire buildings can be printed using concrete-based materials.
- Metal 3D Printing
- Description: Techniques like Direct Metal Laser Sintering (DMLS) and Electron Beam Melting (EBM) enable precise metal part fabrication.
- Applications: Metal 3D printing is extensively used in aerospace and automotive industries for creating lightweight, high-strength components.
- Applications: This technology is revolutionizing healthcare by enabling the production of custom implants, tissue engineering, and drug testing models.
- Sustainable Printing Practices
- Description: Recycled and biodegradable materials are being incorporated to reduce the environmental footprint of 3D printing.
Applications: These practices are particularly important in industries focusing on sustainable manufacturing and reducing waste
Applications of Advanced 3D Printing
- Healthcare
- Custom Prosthetics and Implants: Patient-specific prosthetics and implants are being created with unmatched precision and biocompatibility.
- Tissue Engineering: fabrication of organ models for research and potential transplant solutions.
- Medical Devices: 3D printing is used for rapid prototyping and manufacturing of medical instruments.
- Aerospace
- Lightweight Components: 3D printing produces complex geometries that are lightweight yet strong, essential for fuel-efficient aircraft.
- Spare Parts: On-demand printing of spare parts reduces downtime and inventory costs.
- Rocket Engines: Metal 3D printing is revolutionizing the manufacturing of rocket engine components, enhancing performance and reducing costs.
- Automotive
- Custom Parts: From classic car restorations to innovative designs, 3D printing supports rapid prototyping and production.
- Weight Reduction: The use of lattice structures reduces material usage without compromising strength.
- Electric Vehicles (EVs): Custom battery enclosures and lightweight components improve EV efficiency.
- Construction
- 3D-Printed Homes: Entire structures can now be printed in days using large-scale printers and concrete materials.
- Sustainable Building: The use of recycled materials and energy-efficient designs enhances sustainability.
- Customized Architecture: Unique designs and features can be easily integrated into construction projects.
- Consumer Products
- Personalized Goods: From jewelry to eyewear, 3D printing enables the creation of custom, made-to-order products.
- Footwear: Leading brands use 3D printing for creating customized insoles and shoe designs.
- Household Items: Consumers can print tools, replacement parts, and decorative items at home.
- Electronics
- Flexible Circuits: Advanced printers can produce flexible and stretchable electronic components.
- Embedded Sensors: Functional electronics can be integrated into 3D-printed objects for smart applications.
- with 3D printing for improved comfort and functionality.
Benefits of Advanced 3D Printing
- Design Freedom:
- Complex geometries that are impossible with traditional manufacturing can now be realized.
- Customization:
- Products can be tailored to individual specifications, enhancing user experience.
- Reduced Waste:
- Additive manufacturing uses only the material necessary for the build, minimizing waste.
- Faster Production:
- Rapid prototyping and streamlined production processes reduce lead times.
- Cost Efficiency:
- For small-scale production and prototypes, 3D printing is often more economical than traditional methods.
- Sustainability:
- The integration of recycled and biodegradable materials supports eco-friendly manufacturing practices.
Challenges in 3D Printing
- Material Limitations:
- The range of materials available for 3D printing is expanding but remains limited compared to traditional manufacturing.
- Surface Finish:
- Post-processing is often required to achieve desired surface finishes and tolerances.
- Strength and Durability:
- While improving, 3D-printed parts may not always match the strength of conventionally manufactured counterparts.
- High Costs of Advanced Printers:
- Industrial-grade 3D printers and materials can be prohibitively expensive for small businesses.
- Intellectual Property Concerns:
- The ease of reproducing designs raises issues of copyright and patent infringement.
- Skill Requirements:
- Expertise in design software and printer operation is necessary to maximize the technology’s potential.
Future Trends in 3D Printing
- Integration with AI and Machine Learning:
- Advanced algorithms will optimize designs for performance and manufacturability.
- Hybrid Manufacturing:
- Combining 3D printing with traditional methods will create new possibilities in manufacturing.
- Nanotechnology:
- The development of nano-scale printing technologies will enable ultra-precise manufacturing.
- Global Supply Chain Transformation:
- On-demand local manufacturing will reduce dependency on global supply chains, increasing resilience.
- Expansion of Material Choices:
- Continuous research will lead to a broader range of materials with improved properties.
- Decentralized Manufacturing:
- Distributed 3D printing networks will allow small businesses and individuals to produce high-quality goods.
Conclusion
Advanced 3D printing is revolutionizing manufacturing, enabling innovations that were once thought impossible. From intricate medical devices to large-scale architectural structures, the versatility and potential of this technology continue to grow. While challenges remain, ongoing research and development are paving the way for 3D printing to become an integral part of global industries.
Tags
Related Posts
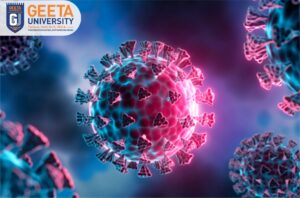
Education trends after Covid 19 – Geeta University
The COVID 19 pandemic flipped the world’s education system upside down this year, causing a significant shift in how pupils learn and teachers teach. Education Trends after Covid 19 The COVID 19 pandemic flipped the world’s education system upside down

The future of Cryptocurrency in India – Geeta University
Gartner, leading research and consulting company, had predicted that the banking industry would receive $ 1 billion in business value in the use of blockchain Crypto currencies by 2022. The Future of Cryptocurrency in India Gartner, leading research and consulting
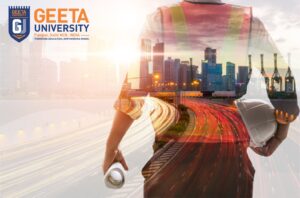
To be a Civil Engineer one must know – Geeta University
Civil engineering is in high demand for work. Working in this field requires very clear skills. It is not easy to find a great civil engineer and the best are richly rewarded. To Be a Civil Engineer one must know